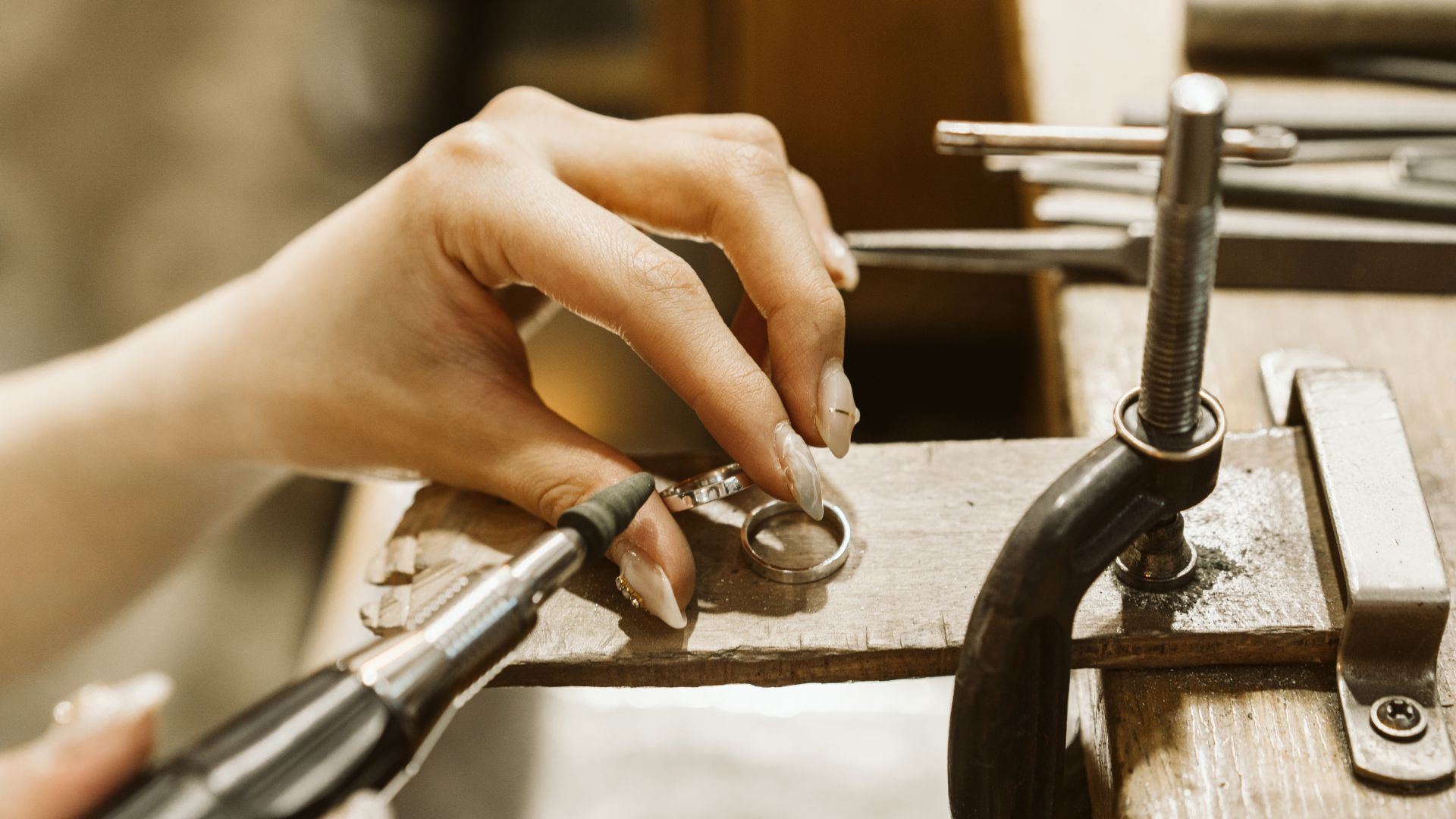
What is lost-wax casting in goldsmithing?
Goldsmithing has a rich history full of fascinating techniques, and one of the most enduring and essential methods still in use today is lost-wax casting. This technique, dating back thousands of years, has been used by artisans to create incredibly intricate jewellery pieces, sculptures, and religious artifacts. It allows goldsmiths to produce detailed designs that would otherwise be difficult or impossible to achieve with traditional methods.
In this article, we’ll explore the lost-wax casting process, its historical significance, and why it remains a cornerstone of modern goldsmithing:
- The lost-wax process
- Advantages and applications
- Challenges and precision
- Why lost-wax casting remains an essential technique in modern goldsmithing
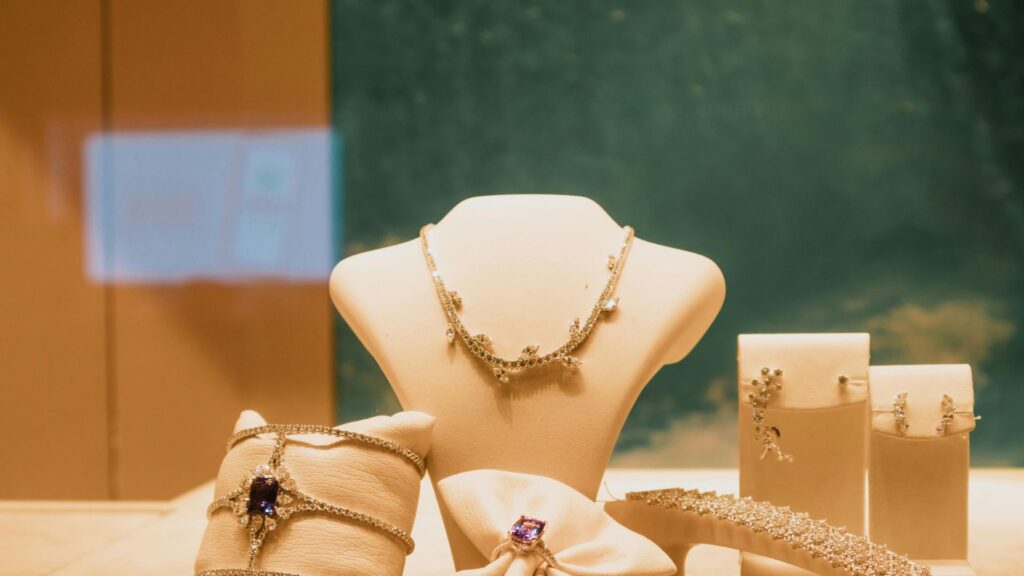
The lost-wax process
The lost-wax casting process is as much an art form as it is a technique, and it involves several steps that must be carried out with precision. Here’s a breakdown of how it works:
1. Creating the wax model
The first step in lost-wax casting is creating a detailed model of the jewellery or object to be cast. This is typically done using a special type of wax, which is malleable and can be carved, shaped, and moulded with precision. The wax model is made as an exact replica of the final design, with all the fine details carefully crafted. If the piece is particularly intricate, multiple layers of wax might be used to build up the model, and fine tools are employed to ensure the exact features of the design are captured.
Once the model is created, it’s important to ensure that it is perfectly smooth and free from imperfections, as these will be replicated in the final metal piece. For this reason, a great deal of care is taken in the wax modelling stage to ensure a flawless design.
2. Creating the mold
After the wax model is complete, it’s time to create the mould. The wax model is first coated in a layer of fine sand or a special type of plaster known as investment. This coating is applied in layers, with each layer allowed to harden before the next one is added. This process helps create a solid, durable mould that will withstand the high temperatures required in the casting process.
The mould is then heated in a kiln to a temperature that causes the wax to melt and drain away. This is the “lost” part of lost-wax casting—the wax is melted and discarded, leaving behind an empty cavity inside the mould that is an exact replica of the original wax model.
3. Pouring the metal
Once the wax has been removed and the mould has cooled, molten metal is poured into the cavity left behind by the wax. Gold, silver, or other metals can be used for the casting, depending on the type of piece being made. The metal is carefully heated until it reaches the appropriate temperature, at which point it is poured into the mould, filling the space left by the melted wax.
As the metal cools and solidifies, it takes on the exact shape and details of the original wax model. This is why precision in the earlier stages of the process is so important—the final metal piece will only be as good as the wax model and the mould that was created.
4. Finishing the piece
After the metal has cooled and solidified, the mould is broken away, revealing the cast metal piece. The jewellery or sculpture will then be cleaned, polished, and any finishing touches, such as stone setting or engraving, will be added. The result is a perfectly cast piece of jewellery or artwork that retains all the fine details of the original design.
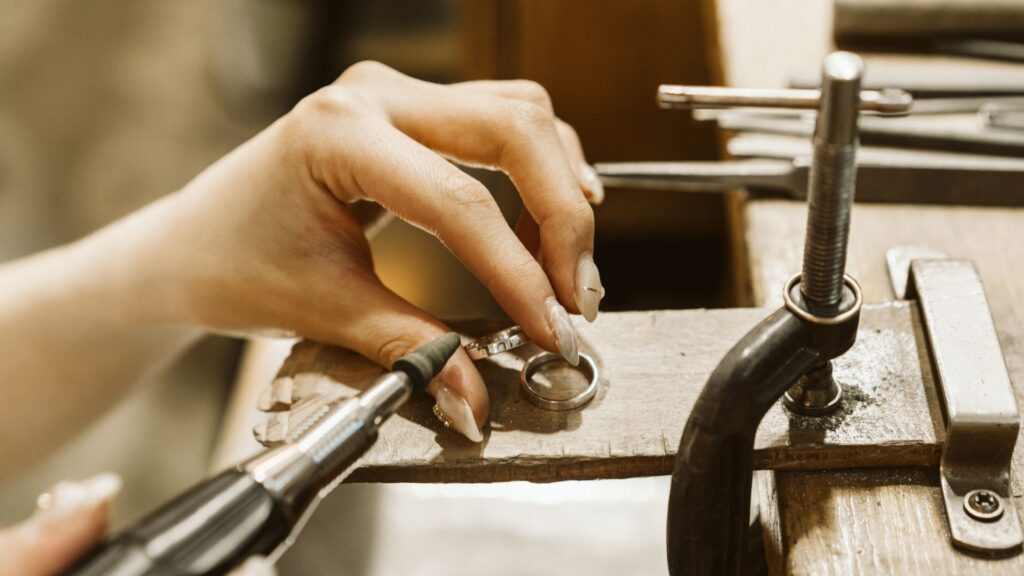
Advantages and applications
One of the main reasons why goldsmiths use lost-wax casting is its versatility. The process allows for incredibly intricate designs that would be very difficult or time-consuming to achieve with traditional handcrafting methods. The level of detail that can be captured in the wax model is astonishing, and this is why it’s so commonly used for fine jewellery and custom pieces. With lost-wax casting, even the smallest design elements, such as delicate textures, tiny engravings, and detailed patterns, can be recreated with remarkable accuracy.
Lost-wax casting also enables the creation of complex shapes that might otherwise require multiple parts to be joined together. The process allows for seamless, continuous pieces without the need for welding or soldering. This makes it particularly useful for creating items like rings, pendants, and sculptures that have intricate designs or unusual shapes.
Furthermore, the process is highly repeatable, which means that once the mould is made, additional copies of the same design can be cast. This is especially useful for producing limited-edition jewellery collections or for creating multiple identical pieces for a client.
Challenges and precision
While lost-wax casting offers numerous advantages, it’s not without its challenges. The process requires a high level of skill and precision, especially in the creation of the wax model and the mould. Any imperfections in the wax model will be reproduced in the final metal piece, so attention to detail is crucial at every step.
One of the biggest challenges in lost-wax casting is ensuring that the mould is free from air pockets or imperfections that could affect the quality of the final piece. The mould must be perfectly smooth and free of flaws to ensure that the molten metal flows evenly and fills the cavity without defects. Similarly, the pouring of the metal must be done with great care to ensure that the metal doesn’t cool too quickly or unevenly, which could cause cracking or other issues.
Additionally, the process of melting the wax and heating the mould requires precise temperature control. Too much heat can cause the mould to break or the metal to become too thin, while too little heat can result in an incomplete casting. This is where the skill and experience of the goldsmith come into play—achieving the perfect conditions is key to producing high-quality results.
Why lost-wax casting remains an essential technique in modern goldsmithing
Despite the many technological advances in goldsmithing, lost-wax casting remains one of the most widely used and respected techniques in the industry. Its ability to produce highly intricate and detailed designs, combined with its versatility in creating complex shapes, makes it an invaluable tool for modern goldsmiths. Whether it’s creating a custom engagement ring, a fine necklace, or a delicate sculpture, lost-wax casting allows goldsmiths to bring their visions to life with unmatched precision.
The process also continues to evolve with the advent of new technologies, such as 3D printing, which is being incorporated into the lost-wax casting process to create even more detailed and complex models. However, the fundamental technique has remained unchanged for centuries, a testament to its enduring value in the world of goldsmithing.
Let’s recap what we learned today:
- The process involves creating a wax model of the design, coating it in a mould, melting the wax away, and pouring molten metal into the cavity to form the final piece.
- Lost-wax casting allows for intricate designs, complex shapes, and seamless pieces, making it ideal for fine jewellery, custom designs, and limited-edition collections.
- The technique is highly versatile, enabling goldsmiths to create detailed textures, engravings, and continuous shapes without the need for welding or soldering.
- The process requires high skill and precision, especially in creating a flawless wax model and mould. Temperature control and avoiding imperfections are critical for high-quality results.
- Despite modern technological advancements, lost-wax casting remains essential in goldsmithing due to its ability to produce detailed, complex designs and its continued evolution with new technologies like 3D printing.
In conclusion, lost-wax casting is not just a technique—it’s an art form that has stood the test of time, enabling goldsmiths to create masterpieces that blend craftsmanship, innovation, and artistry. It’s no wonder that it remains a cornerstone of modern jewellery making, allowing artisans to continue producing exquisite works of art that capture the imagination and stand the test of time.